Professor Ryan Loxton and his research colleagues solve the optimisation problems that overwhelm even high-performance computers. In several Australian industries, the team’s modelling techniques are delivering efficiencies, supporting expansion, and boosting the bottom line.
Loxton is part of Australia’s new generation of research academics that are inspiring university–industry engagement. At Curtin, he fosters collaboration between mathematicians and engineers to improve the efficiency of complex industry processes. Most of the research end-users are in the key Australian export industries of mining, energy and agriculture.
Loxton’s expertise is the design and use of quantitative methods for optimising systems and processes. With his two key colleagues in mathematical sciences, Dr Elham Mardaneh and Dr Qun Lin, Loxton develops novel algorithms and modelling tools for tasks that are beyond the scope of commercially available optimisation software.
“The basic, brute force approach in decision-making is to run through every single possibility, but for industry-scale problems the possibilities explode exponentially,” he explains.
“Without a good algorithm, the computation takes too long.”
“The basic, brute force approach in decision-making is to run through every single possibility, but for industry-scale problems the possibilities explode exponentially. Without a good algorithm, the computation takes too long.”
For example, a few years ago the Marine division of Australia’s largest independent oil and gas company, Woodside, was looking to minimise operating costs off the North West coast of Australia.
The company has a number of offshore oil and gas facilities, comprising platforms as well as floating production, storage and offloading units, each needing regular visits from vessels that deliver essential cargo and assist the transfer of oil to tankers.
The challenge was this: at what times and in what sequence should the support vessels visit each facility? Loxton describes the task:
“Vessel scheduling involves specific operational constraints, such as vessel speeds and capacities, as well as the cargo demands of each facility. In this case, other factors include which vessels have the required equipment, the facility’s closing time and night-time loading restrictions.”
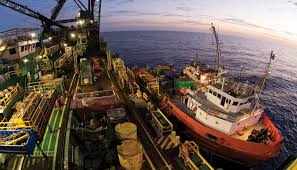
“This is a large-scale problem with millions of variables and constraints. Finding an optimal schedule manually is almost impossible – which is why we design custom mathematical models that can search efficiently through the possibilities.”
For Linkforce, a major Western Australian engineering services company, Loxton led research on optimally scheduling mine plant shutdowns. Once again, the task was to develop and apply customised models to the scheduling process.
“They include a multitude of factors ranging from the availability of personnel to plant activity inter-relationships, and the algorithms take just seconds to run,” Loxton says.
The result is the capability to fast-track mine plant maintenance and minimise downtime – an advance in best practice that not only boosts the plant’s bottom line, but also reduces the environmental footprint of its maintenance activities.
In 2016, the Curtin team was introduced to a very different optimisation challenge – this time from the agriculture sector. Supported by the national Innovation Connections program, WA-based company Global Grain Handling Solutions (GGHS) was looking to develop a tool that enabled farmers to make informed harvesting decisions based on their options for storing the grain. The company’s end goal was to create a simple program that could be used to identify the most profitable scenario for each farm. The task was more complex than you’d imagine – a cost-benefit analysis model involving about 60 input variables, ranging from truck speeds and harvesting rates to grain moisture limits and blending ratios.
Although the Curtin team’s expertise is focused primarily on real-world applications, it is important to acknowledge the fundamental research that underpins the industry impact. Much of this has been supported by the Australian Research Council, through a Postdoctoral Fellowship awarded to Loxton in 2011, followed by an ARC Discovery Project grant.
“I was solving fundamental problems in optimisation and control, using the fellowship opportunity in particular. I was then able to channel those skills into applied research,” he says.
The research also delivered a strong record of research publications – which Loxton says again demonstrates that ‘academic research and industry collaboration are not mutually exclusive spheres’. Between 2011 and 2016, he authored or co-authored 41 publications; among them is a 2013 paper in the prestigious international journal Automatica, describing a new computational method for solving a class of optimal control problems that had received little prior attention. To demonstrate the potential benefits for a range of industries, the research team applied the method to problems in chemical engineering, train control and fisheries.
Collaboration between Woodside and Loxton saw improvements in vessel utilisation and field planning. For Woodside, their initial research collaboration with Loxton (the first of several) led to a significant improvement in vessel utilisation and field planning, delivering a saving of around 20 per cent annually in vessel charter costs across the company’s North West coast facilities. Further demonstrating the project’s success, the method was described in several papers published in optimisation and engineering journals, two co-authored with Woodside personnel.
With a focus on innovation and company expansion, Linkforce took a different path and purchased the IP for the algorithms from Curtin to underpin a software system called Quantum. Commercialised through a new subsidiary company, Onesun, the Quantum software now supports more than 10 projects and 300 end-users in the mining and resources sector. Linkforce expects the technologies will deliver annual cost savings in the tens of millions across the global mining and resources sector. It’s a research success story that embodies the true goals of innovation: to deliver industry and environmental benefits; drive company expansion and employment; and generate further innovation.
Likewise, GGHS is focused on innovation and is progressing commercialisation opportunities with the Curtin team, supported by CSIRO’s ON Prime program. For the Curtin team, the project’s outcome is likely to prompt further collaboration with agricultural industries.
Now an Australian Research Council Future Fellow, Loxton explains why university–industry engagement is essential.
“Australian industries operate in a complex global market; they must modernise their processes and cut inefficiency by exploiting the massive big-data sets now available.
“But the more realistic the model, the more challenging it is to solve. Hence the need for smart algorithms – mathematics is the key to unlocking these massive-scale optimisation problems.”